Technical Blog
How to Choose the Right Joining Method for Small-Diameter Tubing
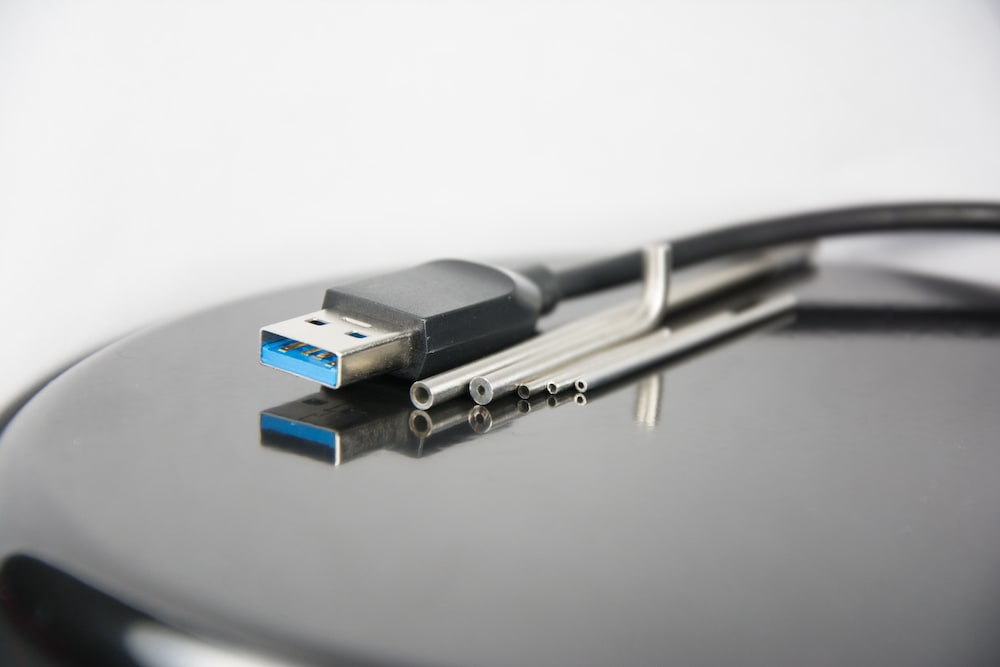
Small-diameter tubing is well-suited for use in flow measurement and sensing, chromatography, aerospace and defense, and alternative energy applications. Even though we manufacture exceptionally long lengths of this type of tubing, their ends still need to be joined. This blog post provides an overview of joining methods, along with some factors to consider so you can get the most out of your tubing investment.
Here’s how the most common connections are made:
- Manual welding: A handheld device creates a clean, square cut on the face of the small-diameter tube. A clamping fixture holds the tubes together, and a tungsten weld head drives an electrode and electric arc around the joint. X-ray inspection verifies weld quality and accuracy.
- Orbital welding: Automated, or orbital, welding offers higher speed, accuracy and repeatability than manual welding. Specifications are stored electronically in the welding machine’s control system to ensure high-quality welds.
- Compression fittings: Designed for easy application, compression fittings consist of a clean tube, a ferrule that seals the tubing and body of the fitting, and a hand-tightened nut to hold the assembly in place. Installation methods can vary by application and tube construction. A gauge is used to measure the fitting.
- Cone and thread, or autoclave, fittings: This joining method is particularly desirable for heavy-walled tubing used to transport high-pressure liquids and gases in R&D applications. As the name implies, the end of the tube is machined into a cone shape, and a left-hand thread is cut into the outside of the tube so a nut can slide onto it. A stopper attaches to the collar to ensure a tight seal.
- Flare, or AN, fittings: Flare fittings trace their origins to World War II, when the United States Army and Navy adopted the standard. In this method, a nut is placed over the tube, and a special tool creates a flare. The interior of the flare is pressed against the male cone to produce the connection. Flare fittings are desirable for mission-critical applications such as aircraft, inaccessible installations or where high pressures or high temperatures are present.
Joining Method Considerations
Welding is typically a slower process than fittings, and it involves more equipment. While automated, or orbital welding, can be faster, it is also more expensive than manual welding, and equipment lead times are longer. Compression fittings are highly versatile and connections are easy. Although the fittings stand up to a variety of conditions, some aggressive fluids can cause corrosion. Compression fittings also require consistently sized tubes so the sections can fit into adjoining segments, and the outer diameters must have a good surface finish. Whichever method you choose, if you bury your tubes underground, be sure to give extra attention to inspections.
Minimize Your Connections
Tubing installations will always require joining. While you can join short lengths of “stick” tubing, seamless coiled tubing offers many advantages. Our long-length, coiled steel tubing requires fewer welds or fittings than joined sections of straight tubing. That means less opportunities for impurities, leaks or other long-term failures. And, fewer joining areas reduces installation time and expenses. Seamless coil tubing is the smart choice for applications requiring small-diameter tubing.
To learn more about HandyTube small-diameter tubing, visit our product page.